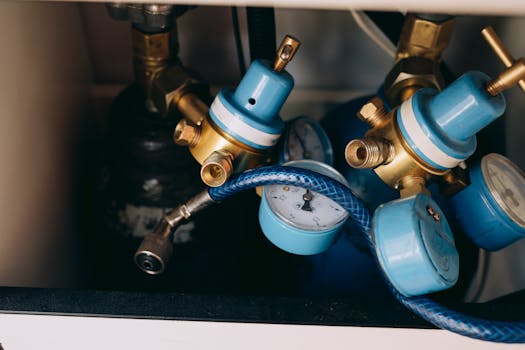
Understanding the Basics of Hydraulics and Pneumatics: A Comprehensive Guide
Takeaways: Hydraulics and pneumatics are two essential technologies that utilize fluids to create motion and power. Hydraulics uses liquids under pressure, while pneumatics uses compressed gases. Understanding these systems is crucial for engineers, technicians, and anyone interested in mechanical systems.
In this article, we will explore the fundamental principles of hydraulics and pneumatics, their applications, and the key differences between them.
What is Hydraulics?
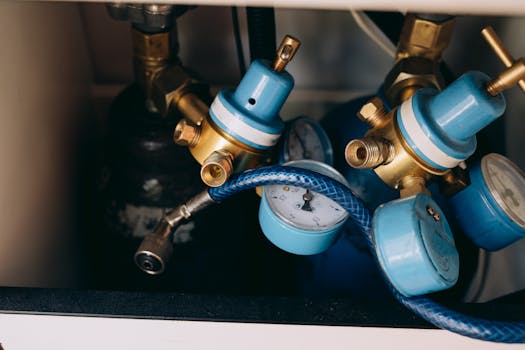
Hydraulic systems are widely used in various applications, including construction machinery, automotive systems, manufacturing, and aerospace. Some common hydraulic components include:
- Hydraulic Pumps: These devices convert mechanical energy into hydraulic energy by moving fluid through the system.
- Hydraulic Cylinders: These are actuators that convert hydraulic energy back into mechanical energy, creating linear motion.
- Hydraulic Valves: Valves control the flow and pressure within the hydraulic system, directing the fluid to where it is needed.
- Hydraulic Accumulators: These devices store energy in the form of pressurized fluid, allowing for a quick release of energy when needed.
Applications of Hydraulics
Hydraulic systems are integral to many industries. In construction, hydraulic excavators and bulldozers rely on hydraulic power to lift heavy loads and perform precise movements. In the automotive industry, hydraulic brake systems ensure safe and effective stopping power.
Additionally, hydraulics play a crucial role in manufacturing processes. For instance, hydraulic presses are used to shape and mold materials under high pressure. In aerospace, hydraulic systems control flight surfaces and landing gear, making them essential for aircraft operation.
What is Pneumatics?
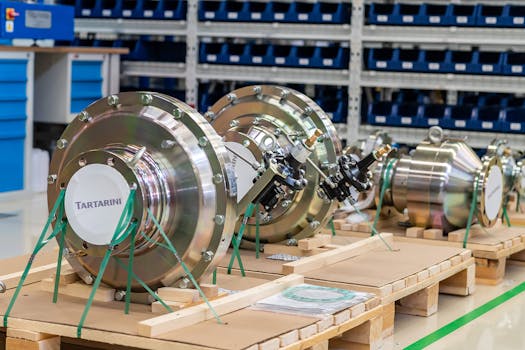
The basic components of pneumatic systems include:
- Air Compressors: These machines convert power into potential energy stored in compressed air.
- Pneumatic Cylinders: These actuate linear motion by using compressed air to push a piston.
- Pneumatic Valves: These control the flow and direction of compressed air in the system.
- Filters and Regulators: These components ensure clean, dry air at the proper pressure for optimal system performance.
Applications of Pneumatics
Pneumatic systems are prevalent in various industries, particularly in manufacturing and automation. They are often used in assembly lines for tasks such as packaging, sorting, and material handling. Pneumatic tools, such as nail guns and impact wrenches, are widely used in construction and maintenance due to their efficiency and ease of use.
Moreover, pneumatic systems are commonly utilized in the food and beverage industry for packaging and bottling processes. Their cleanliness and fast operation make them ideal for environments where hygiene is paramount.
Key Differences Between Hydraulics and Pneumatics
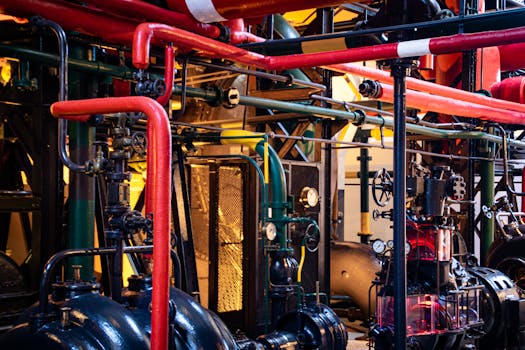
- Medium: Hydraulics uses incompressible liquids, while pneumatics uses compressible gases.
- Pressure Levels: Hydraulic systems typically operate at higher pressures than pneumatic systems, making them suitable for heavy-duty applications.
- Speed: Pneumatic systems generally offer faster response times compared to hydraulic systems.
- Cost: Pneumatic systems tend to be less expensive and easier to maintain than hydraulic systems.
Conclusion
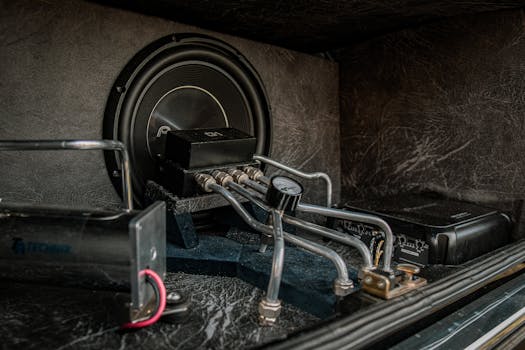