Takeaways
- Hydraulics uses liquid to transmit power, while pneumatics uses compressed air.
- Understanding the principles of fluid mechanics is crucial for both systems.
- Both hydraulics and pneumatics have unique advantages and applications in industry.
Introduction to Hydraulics
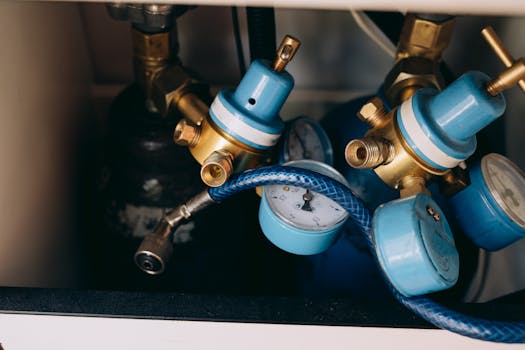
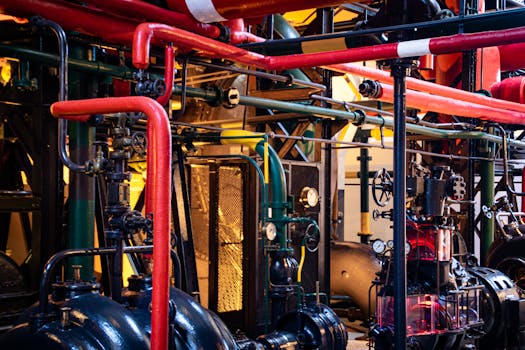
One of the most well-known applications of hydraulics is in heavy machinery, such as excavators and forklifts, where powerful hydraulic systems are used to lift and move heavy loads. The basic components of a hydraulic system include a pump, valves, cylinders, and fluid reservoirs.
Key Components of Hydraulic Systems
1. Pump: The heart of the hydraulic system, the pump moves hydraulic fluid from the reservoir to the rest of the system. Common types of pumps include gear pumps, vane pumps, and piston pumps.
2. Hydraulic Fluid: This is the medium through which power is transmitted. Hydraulic fluids can be oil-based or water-based, and their properties greatly affect system performance.
3. Valves: These control the flow and direction of the hydraulic fluid. They can be manual or automatic and are critical for safely controlling the system’s operation.
4. Cylinders: Hydraulic cylinders convert hydraulic energy into mechanical energy. They are used to create linear motion and can be single-acting or double-acting.
Applications of Hydraulics
Hydraulic systems are widely used in various industries, including construction, manufacturing, and automotive. Some common applications include:
- Construction machinery, such as bulldozers and cranes.
- Manufacturing processes, including injection molding and metal forming.
- Automotive repair equipment, such as hydraulic lifts.
- Flight control systems in aviation.
Introduction to Pneumatics
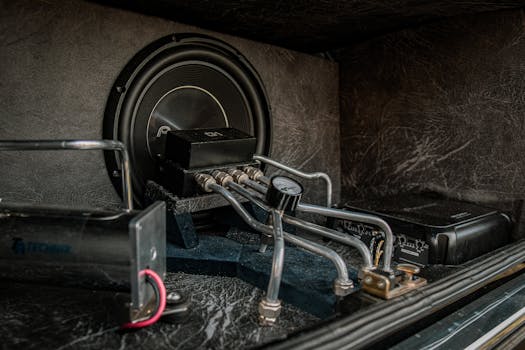
The use of air in pneumatic systems allows for a cleaner and safer working environment, as there is no risk of leaks that can occur with hydraulic fluids. However, pneumatics typically cannot provide the same force output as hydraulics, making them more suitable for lighter applications.
Key Components of Pneumatic Systems
1. Compressor: This is the heart of a pneumatic system, compressing air and supplying it to the system. Compressors come in various types, including reciprocating and rotary screw compressors.
2. Pneumatic Actuators: These devices convert compressed air into mechanical motion. They can be either linear actuators (cylinders) or rotary actuators.
3. Valves: Pneumatic valves control the flow of compressed air within the system. They can be solenoid-operated or manual and are essential for directing airflow to different components.
4. Air Preparation Units: These include filters, regulators, and lubricators that ensure the compressed air is clean, regulated, and properly lubricated for optimal performance.
Applications of Pneumatics
Pneumatic systems are widely utilized in various sectors, including manufacturing, automation, and transportation. Common applications include:
- Assembly line automation for manufacturing products.
- Pneumatic tools, such as drills and wrenches.
- Packaging and material handling equipment.
- Transportation systems, such as pneumatic tubes for parcel delivery.
Comparing Hydraulics and Pneumatics
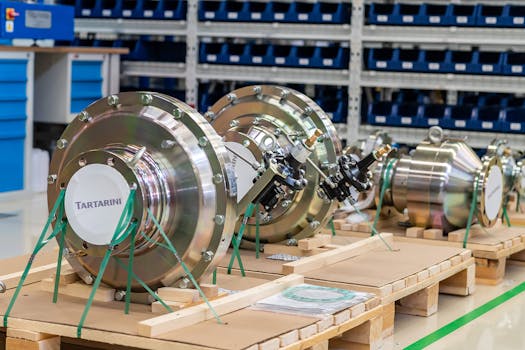
1. Medium: Hydraulics uses incompressible liquids, while pneumatics uses compressible gases (air).
2. Force Output: Hydraulic systems can generate much higher forces compared to pneumatic systems, making them suitable for heavy lifting tasks.
3. Speed: Pneumatics generally provide faster movements due to the compressibility of air, making them ideal for applications requiring quick cycles.
4. Environment: Pneumatics are often preferred in clean environments, while hydraulics can be more robust but may pose risks of leaks.
Conclusion
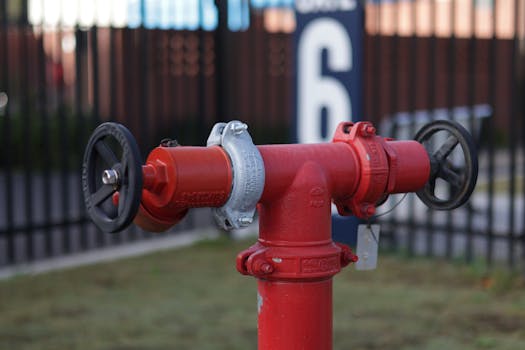