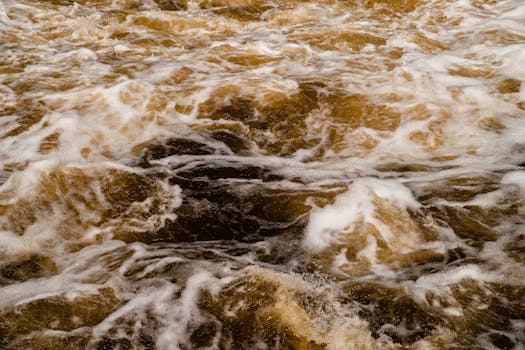
Understanding the Basics of Hydraulics and Pneumatics: A Comprehensive Guide
Takeaways: Hydraulics and pneumatics are essential technologies in modern engineering, utilizing fluids to transmit power and perform work. This article covers the basic principles, differences, and applications of both systems to provide a solid foundation for understanding these critical technologies.
Hydraulics and pneumatics are two branches of fluid power technology that play a crucial role in various industrial applications. While they share some similarities, they operate on different principles and use different types of fluids. This article aims to provide a comprehensive overview of both hydraulics and pneumatics, exploring their basic principles, components, and applications.
What is Hydraulics?
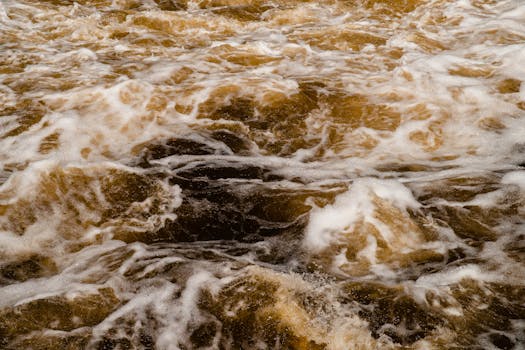
Hydraulic systems typically use incompressible fluids, such as oil or water, to transfer energy. The primary components of a hydraulic system include:
- Hydraulic Pump: Converts mechanical energy into hydraulic energy by pressurizing the fluid.
- Hydraulic Cylinder: Converts hydraulic energy back into mechanical energy, creating linear motion.
- Hydraulic Motor: Similar to a hydraulic cylinder but converts hydraulic energy into rotational motion.
- Valves: Control the flow and direction of the hydraulic fluid.
- Reservoir: Stores the hydraulic fluid.
Hydraulic systems are widely used in various applications, including construction machinery (excavators, loaders), manufacturing equipment (presses, rollers), and automotive systems (brakes, steering). They are valued for their ability to generate high force in a compact design, making them ideal for heavy-duty applications.
What is Pneumatics?
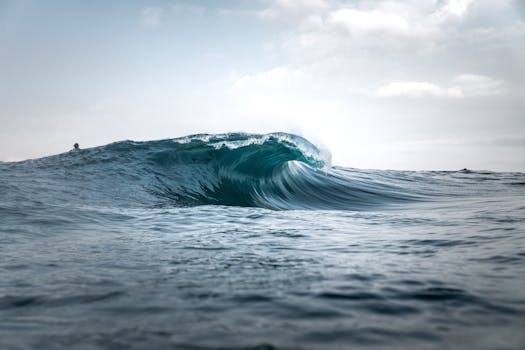
Key components of a pneumatic system include:
- Air Compressor: Compresses atmospheric air and stores it in a tank.
- Pneumatic Cylinder: Converts compressed air into mechanical motion, typically linear motion.
- Pneumatic Motor: Converts compressed air into rotational motion.
- Valves: Control the flow and direction of the compressed air.
- Filters and Regulators: Ensure that the compressed air is clean and at the correct pressure.
Pneumatic systems are commonly used in applications such as automation (robotic arms, assembly lines), handling equipment (conveyor systems), and tools (pneumatic drills, impact wrenches). They are preferred for their speed, ease of maintenance, and safety in environments where electrical equipment may pose a risk.
Key Differences Between Hydraulics and Pneumatics
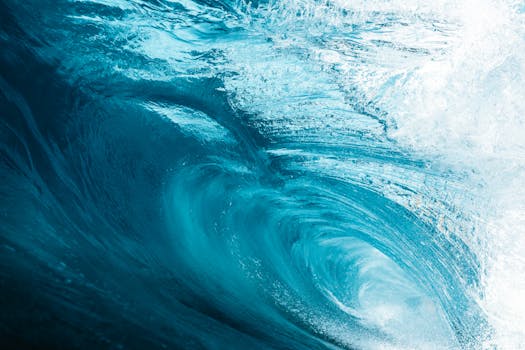
- Fluid Type: Hydraulics use liquids, while pneumatics use gases.
- Compressibility: Liquids are incompressible, making hydraulics more efficient for high-force applications. Gases are compressible, which can lead to a delay in response in pneumatic systems.
- Force Generation: Hydraulic systems can generate much higher forces compared to pneumatic systems, making them suitable for heavy machinery.
- Speed and Control: Pneumatic systems typically offer faster operation speeds and easier control, making them ideal for automation and repetitive tasks.
Conclusion
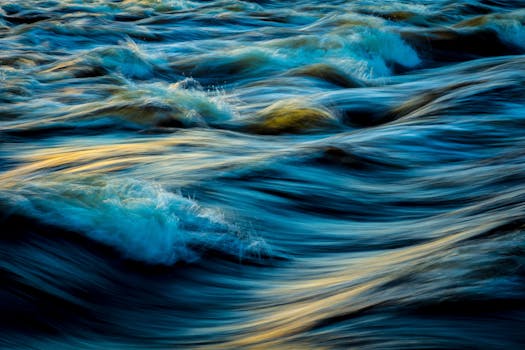