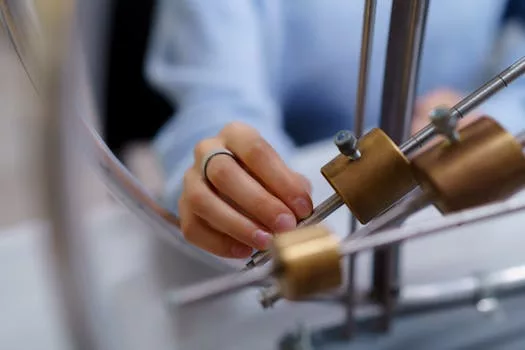
Common Mechanical Failures and How to Troubleshoot Them
Takeaways: Mechanical failures can lead to costly downtime and repairs. Understanding the common types of failures and mastering troubleshooting techniques can save time and money. This article provides insights into the most frequent mechanical issues and effective approaches to diagnose and fix them.
In any industry that relies on machinery, mechanical failures can halt operations, leading to significant financial losses. This article will explore some of the most common mechanical failures, their symptoms, and practical troubleshooting techniques to resolve these issues. Whether you are an engineer, technician, or a DIY enthusiast, this guide aims to equip you with the knowledge needed to effectively tackle mechanical problems.
1. Understanding Common Mechanical Failures
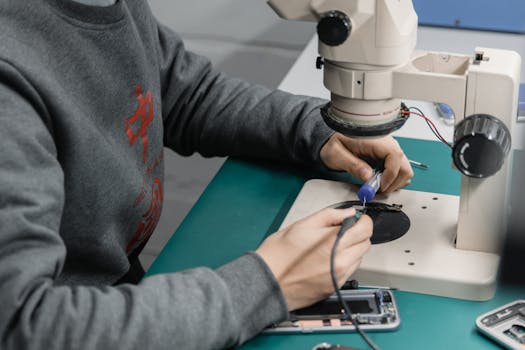
A. Wear and Tear
Over time, parts in machines and equipment can wear down due to friction and repeated use. Common components that experience wear and tear include bearings, gears, and seals. Symptoms of wear and tear may include unusual noises, vibrations, or decreased performance.
B. Misalignment
Misalignment occurs when components that should be parallel or perpendicular are not properly aligned. This can lead to increased wear, overheating, and ultimately, failure of the components involved. Signs of misalignment include excessive vibration and abnormal heat generation.
C. Lubrication Failure
Proper lubrication is essential for the smooth operation of machinery. Lack of lubrication can lead to overheating, increased friction, and wear on moving parts. Symptoms of lubrication failure include squeaking noises, overheating components, and visible wear on parts.
D. Electrical Failures
Many mechanical systems rely on electrical components to function correctly. Electrical failures can manifest as power loss, short circuits, or faulty sensors. Symptoms may include erratic behavior of equipment or failure to start.
2. Troubleshooting Techniques
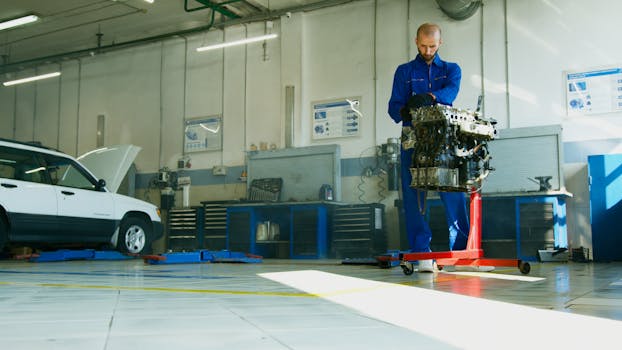
A. Visual Inspection
The first step in troubleshooting is to conduct a thorough visual inspection of the machinery. Look for signs of wear, misalignment, or damage. Check for leaks, loose connections, or any foreign objects that may be obstructing components.
B. Listen for Unusual Noises
Pay attention to the sounds that the machinery makes during operation. Unusual noises such as grinding, squeaking, or rattling can indicate specific problems. For instance, a grinding noise may suggest a misalignment, while a squeaking sound may point to lubrication issues.
C. Monitor Performance Metrics
Utilize performance metrics to identify abnormalities. Monitor temperature, speed, and vibration levels. If any of these metrics fall outside normal ranges, further investigation is required to pinpoint the issue.
D. Consult the Manual
Always refer to the equipment’s manual for troubleshooting guidance. Manuals often contain valuable information regarding common issues and suggested solutions. They may also provide troubleshooting flowcharts that can help narrow down the problem.
E. Systematic Testing
When all else fails, conduct systematic tests. Isolate components and test them individually to determine which part is malfunctioning. This may involve using specialized tools such as multimeters for electrical issues or vibration analyzers for mechanical problems.
Conclusion
