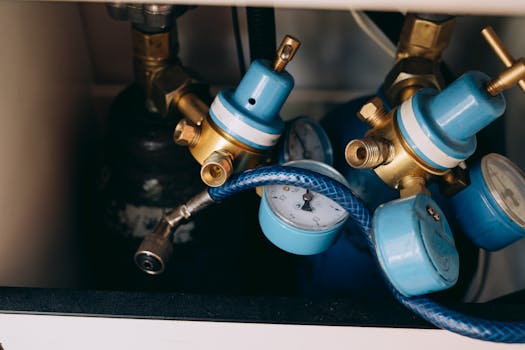
Understanding the Basics of Hydraulics and Pneumatics
Takeaways: Hydraulics and pneumatics are two critical technologies used in various engineering applications. Hydraulics uses liquids under pressure, while pneumatics uses compressed gases. Understanding these principles is essential for anyone involved in engineering, manufacturing, or maintenance.
In this article, we will explore the fundamental concepts of hydraulics and pneumatics, their applications, advantages, and how they differ from each other.
What is Hydraulics?
Hydraulics is a technology that utilizes incompressible fluids, usually oil or water, to transmit power. The basic principle of hydraulics is based on Pascal’s Law, which states that a change in pressure applied to an enclosed fluid is transmitted undiminished throughout the fluid. This allows for efficient energy transfer and is commonly used in heavy machinery, automotive systems, and various industrial applications.
Key Components of Hydraulic Systems
- Hydraulic Fluid: The medium through which power is transmitted. It is essential for lubricating components and preventing wear.
- Hydraulic Pump: Converts mechanical energy into hydraulic energy by moving the hydraulic fluid through the system.
- Actuators: Devices such as hydraulic cylinders or motors that convert hydraulic energy back into mechanical energy.
- Valves: Control the flow and direction of the hydraulic fluid within the system.
- Reservoir: Stores the hydraulic fluid and helps maintain the system’s pressure.
Applications of Hydraulics
Hydraulic systems are widely used in various industries. Here are some common applications:
- Construction Equipment: Hydraulic excavators, bulldozers, and cranes rely on hydraulic systems for lifting and moving heavy loads.
- Automotive Industry: Brake systems and power steering utilize hydraulics for improved control and safety.
- Aerospace: Aircraft landing gear and control systems often employ hydraulic mechanisms for reliability and precision.
- Manufacturing: Hydraulic presses are used in metal forming, plastic molding, and many other manufacturing processes.
What is Pneumatics?
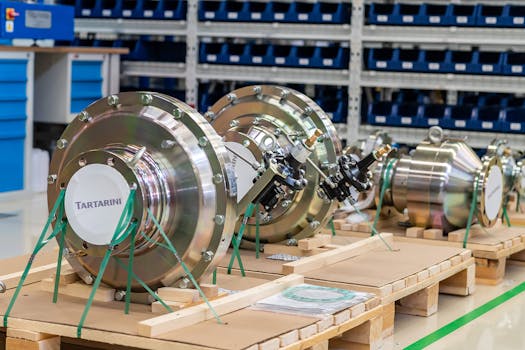
Key Components of Pneumatic Systems
- Compressor: Generates compressed air and maintains the pressure within the system.
- Pneumatic Actuators: Devices such as cylinders and motors that convert compressed air into mechanical motion.
- Valves: Control the flow of compressed air and the operation of actuators.
- Air Treatment Units: Include filters, regulators, and lubricators to ensure clean and properly conditioned air.
Applications of Pneumatics
Pneumatic systems are widely used in various applications, including:
- Manufacturing: Automation systems, robotic arms, and assembly lines often use pneumatics for speed and efficiency.
- Transportation: Pneumatic brakes in trains and buses enhance safety and performance.
- Food and Beverage Industry: Pneumatic systems are used for packaging and conveying products due to their cleanliness and ease of maintenance.
Comparing Hydraulics and Pneumatics
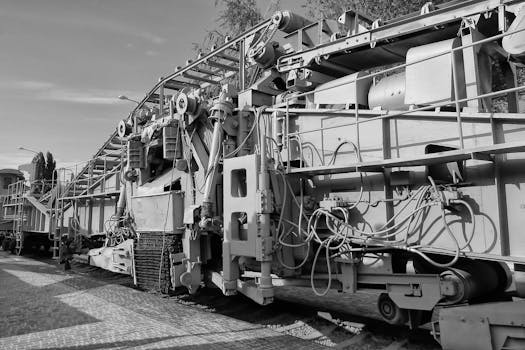
- Medium: Hydraulics uses liquids, while pneumatics uses gases.
- Power: Hydraulics can generate greater force and handle heavier loads due to the incompressibility of liquids.
- Speed: Pneumatics typically operates faster because gases can be compressed and moved more quickly.
- Applications: Hydraulics is preferred for heavy machinery, while pneumatics is more common in lightweight systems and automation.
Conclusion
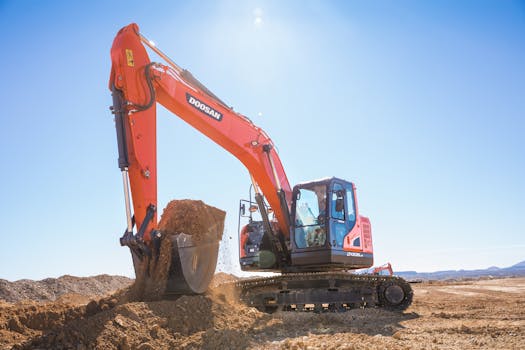