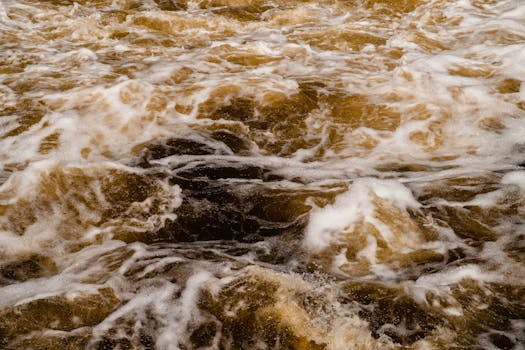
Understanding the Basics of Hydraulics and Pneumatics: A Comprehensive Guide
Takeaways:
- Hydraulics uses liquids to transmit power, while pneumatics uses gases.
- Both systems are essential in automation and machinery.
- Understanding the differences can help in selecting the right system for specific applications.
Hydraulics and pneumatics are two vital fields in engineering that deal with the transmission of power through fluids. While they may seem similar at first glance, they serve different purposes and have distinct characteristics. In this article, we will delve into the basics of hydraulics and pneumatics, explore their applications, and highlight their key differences.
What is Hydraulics?
Hydraulics refers to the use of incompressible fluids, usually liquids, to transmit power. The fundamental principle behind hydraulics is Pascal’s Law, which states that pressure applied to a confined fluid is transmitted undiminished throughout the fluid. This principle enables hydraulic systems to lift heavy loads or perform work efficiently.
The components of a hydraulic system typically include:
- Hydraulic Fluid: A liquid, often oil, that transmits power and lubricates components.
- Hydraulic Pump: Converts mechanical energy into hydraulic energy by pressurizing the fluid.
- Actuators: Devices such as hydraulic cylinders or motors that convert hydraulic energy back into mechanical energy.
- Valves: Control the flow and direction of the hydraulic fluid.
Hydraulic systems are commonly used in various applications, including:
- Construction Equipment: Excavators, backhoes, and bulldozers rely on hydraulic systems for their operation.
- Manufacturing: Hydraulic presses and assembly machines utilize hydraulic power for shaping and assembling parts.
- Aerospace: Hydraulic systems play a crucial role in aircraft control surfaces and landing gear operations.
What is Pneumatics?
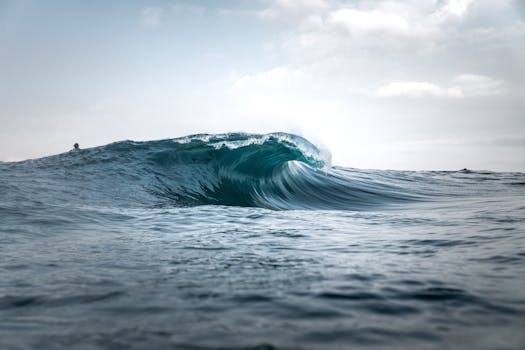
A typical pneumatic system consists of:
- Compressor: A machine that compresses air to create a reservoir of high-pressure gas.
- Pneumatic Actuators: Devices like cylinders that convert compressed air into linear or rotary motion.
- Control Valves: Manage the flow of compressed air to actuators.
- Air Treatment Units: Filters, regulators, and lubricators to ensure clean and properly conditioned air.
Pneumatic systems are widely used in industries such as:
- Automation: Pneumatic actuators are commonly found in assembly lines and robotic systems.
- Packaging: Many packaging machines utilize pneumatic systems for efficiency and speed.
- Material Handling: Pneumatic conveyors transport materials using compressed air.
Key Differences Between Hydraulics and Pneumatics
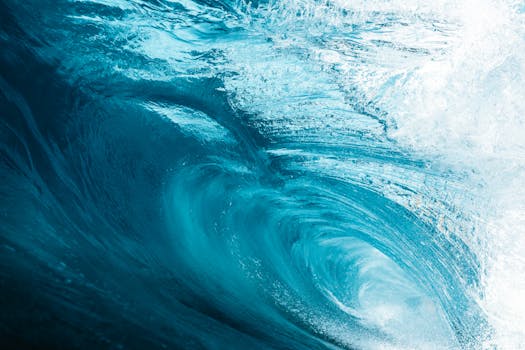
- Medium: Hydraulics uses liquids, while pneumatics uses gases.
- Pressure Range: Hydraulic systems typically operate at higher pressures (up to thousands of psi), while pneumatic systems operate at lower pressures (usually under 150 psi).
- Speed: Pneumatic systems can achieve faster movements due to the compressibility of gases, while hydraulic systems are better for heavy lifting.
- Complexity: Hydraulic systems tend to be more complex and require more maintenance than pneumatic systems.
- Applications: Hydraulics is preferred for heavy-duty applications, whereas pneumatics is favored for lighter, faster tasks.
Conclusion
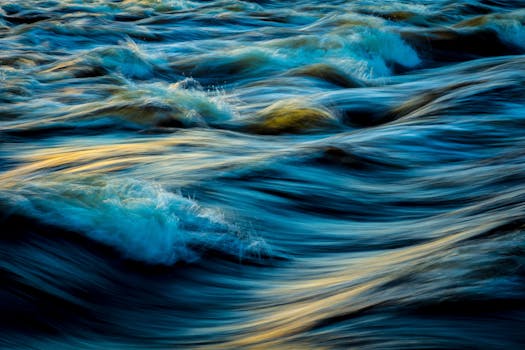