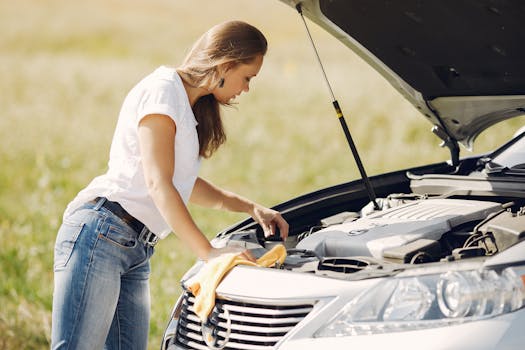
Troubleshooting Common Mechanical Failures: A Comprehensive Guide
Takeaways: Understanding common mechanical failures and knowing how to troubleshoot them can save you time and money. Regular maintenance is key to preventing these issues, and effective troubleshooting techniques can help you identify and resolve problems quickly.
In this article, we will delve into the most frequent mechanical failures, offer troubleshooting strategies, and provide tips on how to maintain your equipment to avoid these issues in the future.
Understanding Common Mechanical Failures
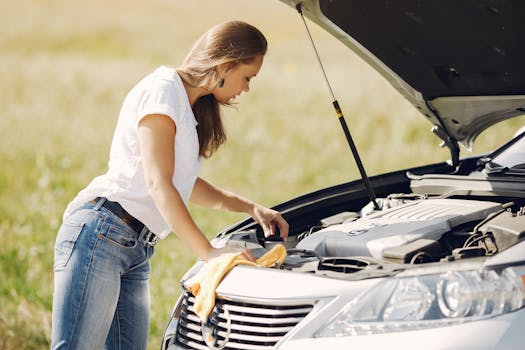
- Overheating: This can be caused by insufficient lubrication, excessive load, or environmental factors.
- Vibration: Excessive vibration may indicate imbalance, misalignment, or worn bearings.
- Leaks: Fluid leaks can occur due to worn seals or fittings, leading to loss of pressure and efficiency.
- Stalling: This can happen when a mechanical component fails to operate under load due to various reasons, including electrical issues.
Troubleshooting Techniques
When faced with mechanical failures, a systematic approach to troubleshooting is essential. Here’s how to tackle common issues:
1. Overheating
If your machinery is overheating, start by checking the lubrication levels. Make sure that all moving parts are adequately lubricated. Inspect the air filters and vents to ensure they are not clogged, which can obstruct airflow and cooling. Additionally, verify that the load on the machine is within operational limits.
2. Vibration
Excessive vibration can lead to severe damage if not addressed. Begin by checking for any loose components or fasteners. Use a vibration analyzer to identify the frequency and amplitude of the vibrations, which can help pinpoint the source of the problem. Examine the alignment of rotating components and adjust if necessary.
3. Leaks
To troubleshoot leaks, first identify the source by cleaning the area around the leak and monitoring for fresh fluid. Check all seals and gaskets for wear and replace them as needed. Ensure that fittings are tight and secure. For hydraulic systems, inspect hoses for cracks or damage.
4. Stalling
If your machinery is stalling, check for electrical issues first. Ensure that all connections are secure and that the power supply is stable. Inspect for any signs of wear on electrical components and replace them if necessary. Additionally, confirm that the mechanical load is appropriate for the equipment.
Preventive Maintenance Tips
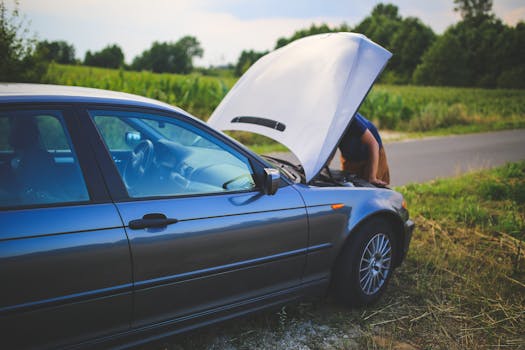
- Regular Inspections: Schedule frequent inspections to catch potential issues early.
- Lubrication: Keep all moving parts well-lubricated to reduce friction and wear.
- Training: Ensure that all operators are trained on proper use and maintenance of machinery.
- Documentation: Maintain a log of all maintenance and repairs for tracking purposes.
Conclusion
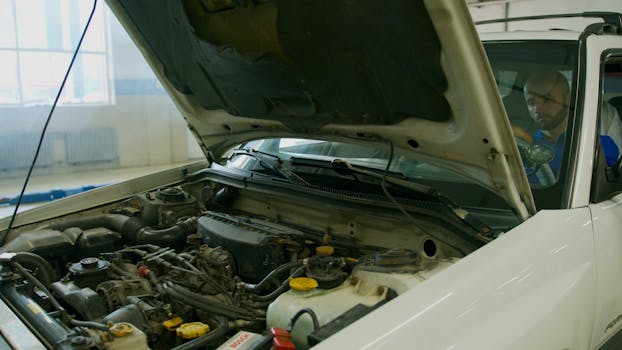